Achieving negative emissions in a hard-to-abate sector
This content was paid for by NGK Insulators and produced in partnership with the Financial Times Commercial department.
In 1970, the US federal government passed the Clean Air Act, which established air quality standards regulating pollution from industry and transport. This landmark law has been emulated by governments worldwide ever since, contributing to better air quality for billions of people.
Significantly, the legislation also spurred technical innovations to meet environmental goals without sacrificing growth. One of these innovations is the catalytic converter, fitted onto automotives with internal combustion engines to reduce harmful emissions. As a result, tailpipe emissions from passenger vehicles are 99 per cent cleaner for most pollutants compared to the 1960s.
One of the largest global manufacturers of substrates used in such catalytic converters today is NGK Insulators Ltd., the Japanese technology company.
NGK’s president Shigeru Kobayashi likes to talk about senator Edmund Muskie of Maine, who authored the Clean Air Act and became a leading voice of modern American environmentalism. Kobayashi sees similarities between the developments in the 1970s in air pollution regulation and the current pivot to carbon neutrality. He believes the new global commitment to cutting GHG emissions will spur new innovations, including many in ceramics.
“Reducing and regulating the emissions of CO2 is now the key issue and clearly where the business opportunities are,” says Kobayashi. “I believe we have many ceramic-based technologies that can effectively contribute to decarbonisation and efforts to capture, store and utilise carbon sustainably.”
Ceramic solutions for CCUS
Indeed, NGK has a surprisingly broad portfolio of potential solutions across the carbon, capture, utilisation and storage (CCUS) cycle.
The company is working on ceramic membranes capable of separating substances at a molecular level, including carbon dioxide, with unique sub-nanometre-sized pore control technology. It is already field testing one of these membranes to separate CO2 during enhanced oil recovery processes. In addition, it hopes to develop others that can capture CO2 directly from factory and energy plant flues. And for the vast amounts of CO2 already released into our atmosphere, the company is developing a honeycomb-structured ceramic contactor for use in direct air capture (DAC).
Captured carbon in these processes can then be used to generate various synthetic fuels such as methane, methanol and e-fuels.
Finally, to power various steps of this cycle, the company is offering grid-scale ceramic-based NAS* storage batteries that have been successfully deployed for over 20 years. It is also developing a new zinc rechargeable ZNB battery optimised for safe indoor use.
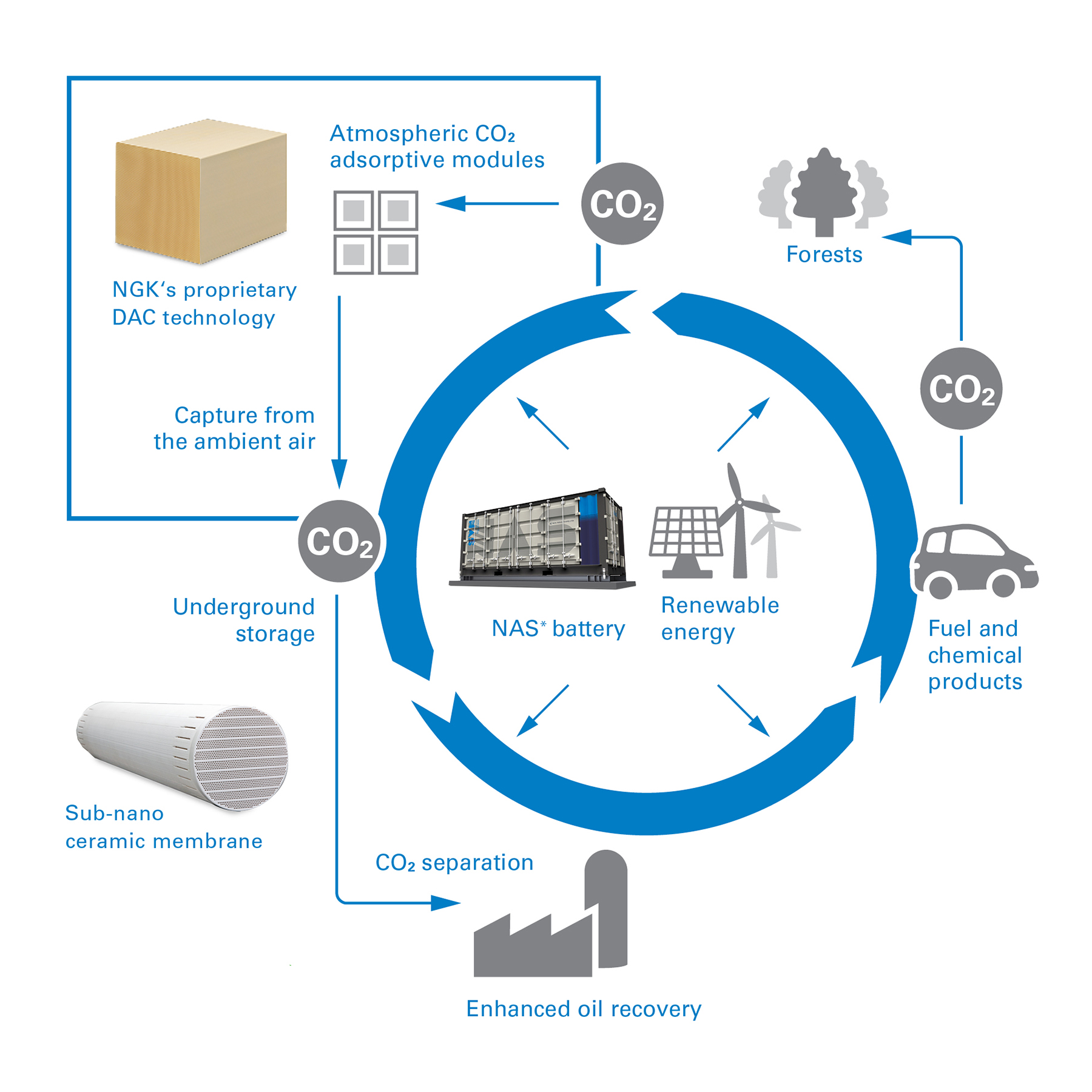
“All of these key technologies — from membranes, reactors, to honeycombs — have evolved out of producing catalytic converters for the automotive industry,” says Kobayashi. “So we already have the know-how, factories, people and capital needed for massive scaling of these solutions.”
Ceramics can improve energy efficiency and structural durability
It makes sense for a company to be eager to refashion its production lines, which annually supply tens of millions of components to internal combustion engine automobiles, towards products aimed at a carbon-neutral future.
But even from a purely technical perspective, ceramics offer advantages. Compared to organic materials currently being used for various CCUS processes, ceramic membranes can more accurately separate out carbon, hence making them more energy efficient. In addition, when used as a component for DAC, the inherent chemical and physical stability of ceramics structures contributes to a longer service life than rival technologies in pellet and fibre form.
“Ceramic membranes and filters can be used efficiently under high temperature, high pressure, and corrosive environments, while also providing efficient and highly accurate separation of particles, including for CO2,” explains Kobayashi.
Another consideration is that ceramic products can be made from a material that is abundant and commonly available. For example, NGK’s ceramic-based NAS* batteries, which do not use rare metals, will become increasingly attractive as global lithium supplies come under strain from surging demand.
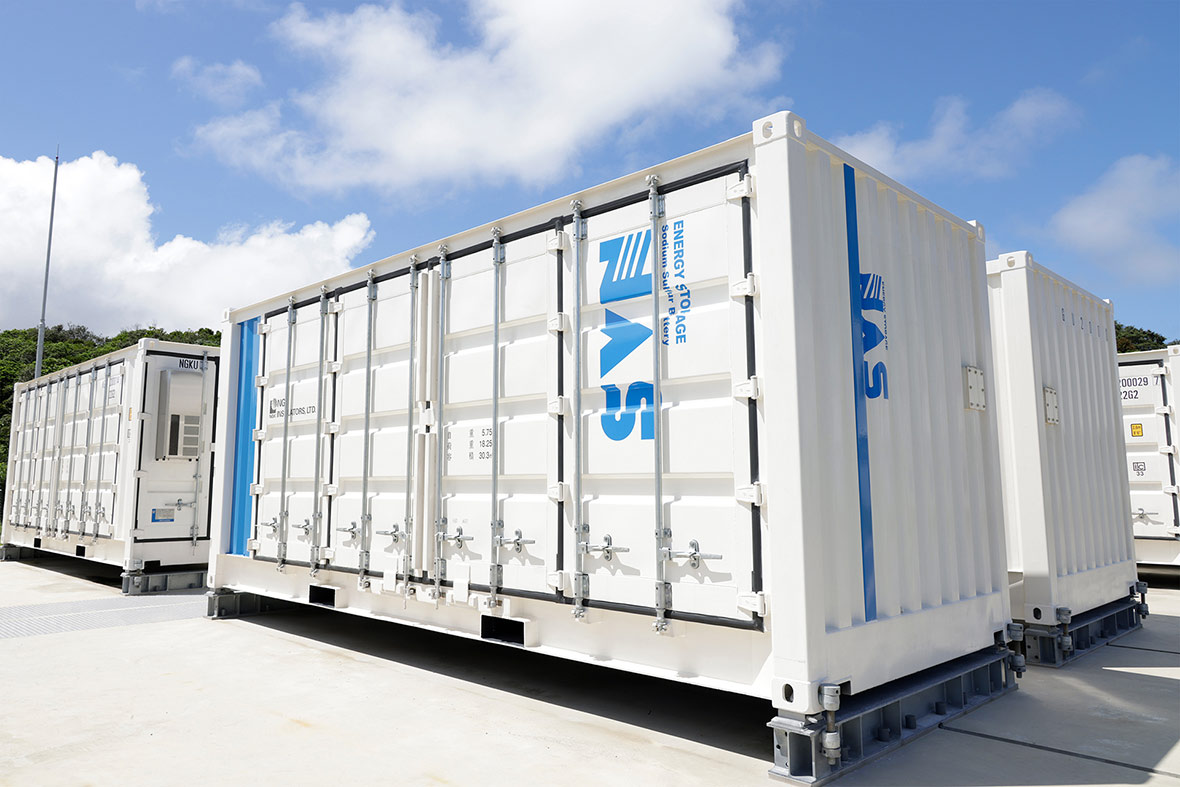
To work towards its new vision as a leader of carbon-neutral and digital technologies, NGK will spend ¥300bn over the ten-year period to 2030 on R&D for solutions related to these two fields. The goal is to generate half of its total sales from products from these areas by 2030, and to then raise it to 80 per cent by 2050 from its current 30 per cent.1
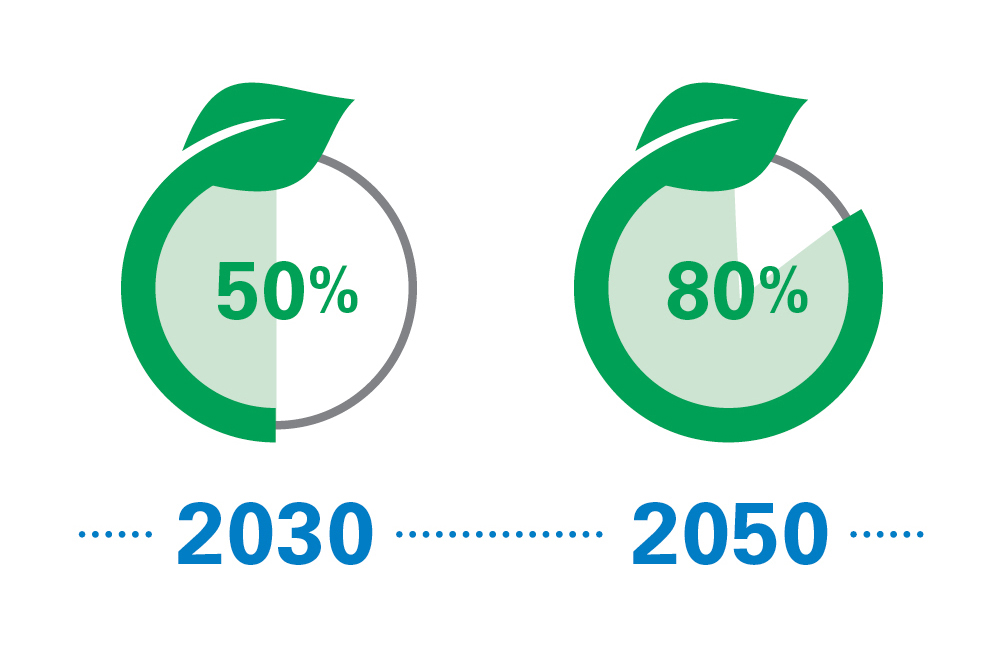
The company also expects steady demand for automotive catalysts as exhaust regulations across developing world markets become more stringent, and the shift to EVs has yet to materialise. Elsewhere, sales from semiconductor manufacturing equipment materials and various electronic components are robust, in line with the ongoing digital transformation of the global economy.
Bringing a hard-to-abate sector to zero emissions
One key challenge in achieving net zero emissions is ensuring the technology used to capture carbon does not generate more carbon than it captures. This challenge is particularly relevant for ‘hard-to-abate’ sectors like steel, cement and chemicals, which are energy-intensive and have hefty emissions.
Ceramic manufacturing is an energy-hungry industry, with high-tech industrial ceramics often fired at over 1,300 degrees Celcius inside furnaces primarily fuelled by burning natural gas. Today, industrial ceramics account for some 1 per cent of Europe’s carbon emissions.
NGK figures show the company emitted, at its peak level, 870,000 tonnes of CO2 in 2019 (of which 70 per cent came from electricity and 30 per cent from fossil fuels used for kilns). The firm says it is working to reduce emissions to 370,000 tonnes of CO2 by 2030 and reach net zero by 2050.2
“We have been experimenting with hydrogen to fire our kilns and find that it is more or less possible,” explains Kobayashi. “But for this fuel transition to be feasible, there needs to be a supply chain of cheap and clean hydrogen.”
Last year, NGK joined the RE100, a global initiative which aims for 100 per cent of the electricity used in business operations to come from renewable energy sources. As a result, the company has committed to sourcing all electricity in its overseas operations from renewables by 20253 and globally by 20404. To accelerate this process, NGK is deploying large-scale NAS* storage batteries in combination with photovoltaic cells across its factories globally, with a target of generating some 40MW (amounting to a cut of 22,000 tonnes of CO2 emissions) from its own solar panels by 20255.
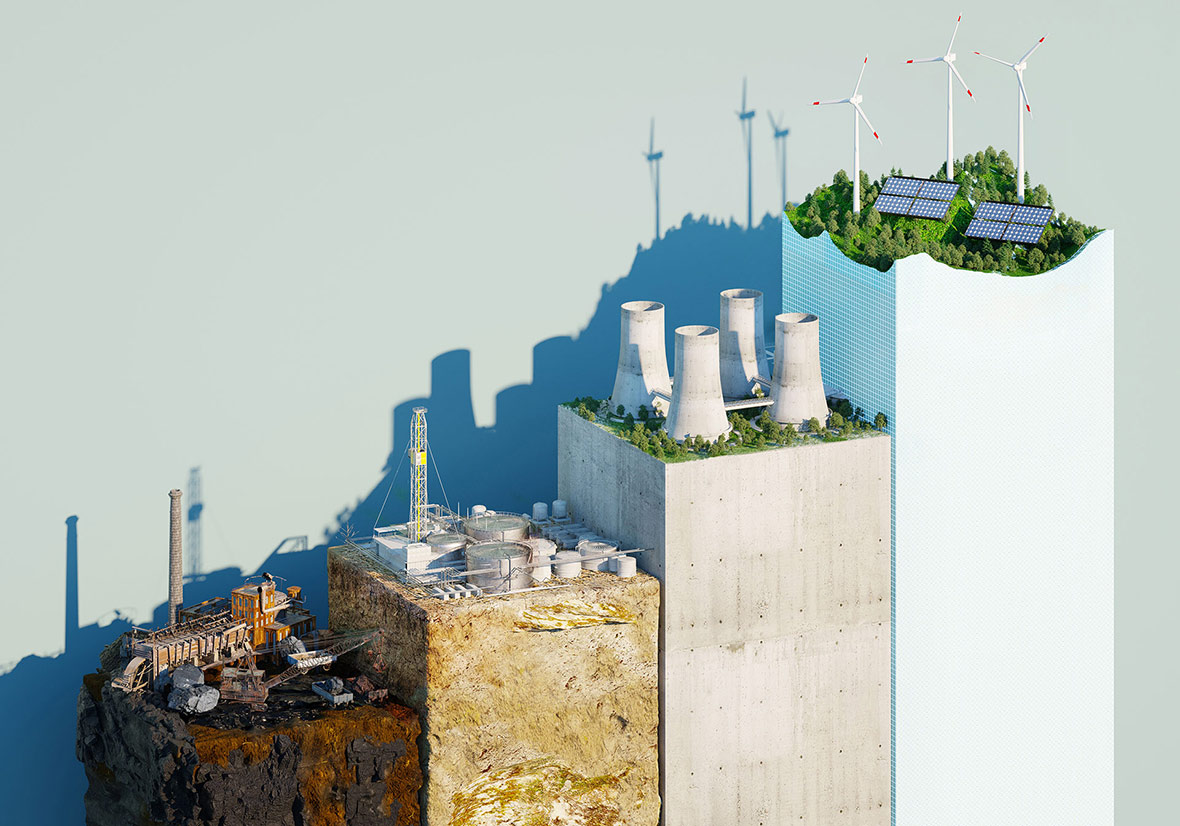
Much remains to be done, but the tempo for this century-old ceramics specialist is accelerating.
“There are few companies like us which have been patiently, almost boringly, researching ceramic technologies for decades,” says Kobayashi. “Now, we are combining this with a focus on agility to bring these solutions to market quickly.”
NAS is a trademark of NGK Insulators, Ltd., registered in the US and other countries