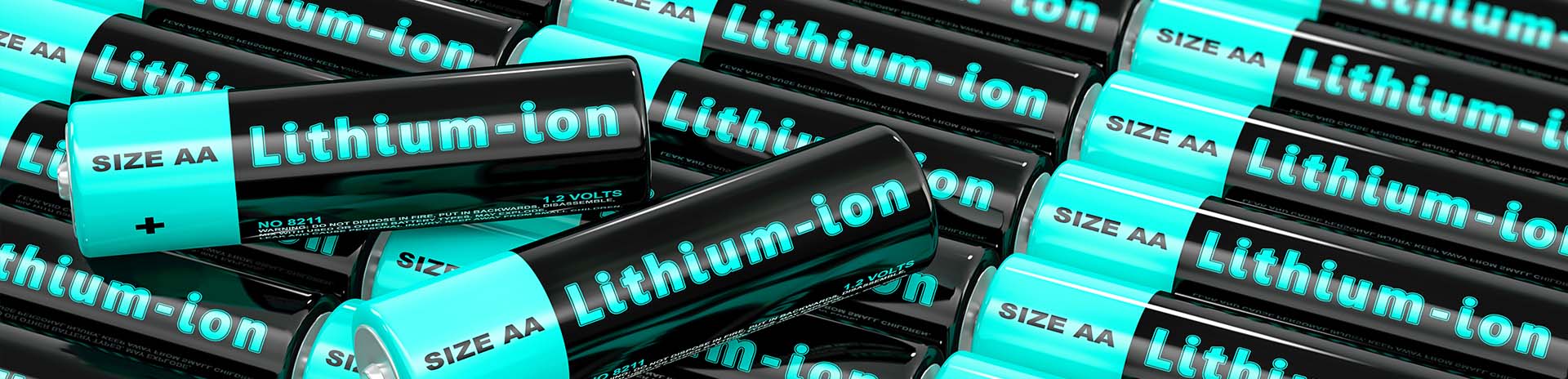
Featured Articles
Continuous Drying Furnaces for Lithium-Ion Battery Electrode Substrate Dehydration (Absolute Drying) Processes
Achieving a Continuous Dehydration (Absolute Drying) Process
NGK has successfully combined its proprietary wavelength-control heater with a slalom configured roll-to-roll furnace that allows continuous conveying, transforming the conventional batch process for lithium-ion battery electrode substrate dehydration into a continuous process. This eliminates deformation defects and reduces drying times, revolutionizing the manufacturing process.
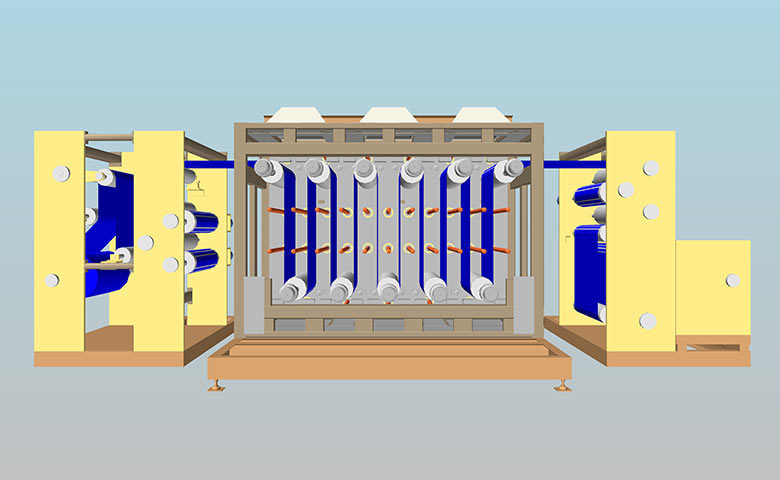
Conventional Lithium-Ion Battery Electrode Substrate Dehydration (Absolute Drying) Process and Issues Involved
The most common lithium-ion battery electrode substrate dehydration (absolute drying) process is vacuum batch drying. Vacuum batch drying raises the following issues:
(1)Dehydration (absolute drying) processing is performed in batches
Using vacuum batch drying furnaces for dehydration (absolute drying) processes creates the following issues due to the long processing times required for vacuum batch drying furnaces:
- Roll inventory awaiting drying builds up, forming bottlenecks.
- A drying chamber is required for the roll inventory. This chamber takes up space and requires temperature and humidity control.
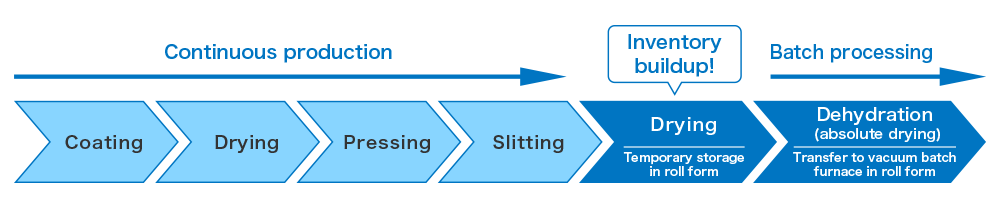
(2)Dehydration processing in roll form
Using vacuum batch drying furnaces for dehydration (absolute drying) processes creates the following issues due to dehydration being performed in roll form:
- Productivity is reduced by the long processing time taken until complete dehydration (absolute drying).
- Drying in roll form results in uneven drying between the roll exterior and center.
- Drying in roll form and in a vacuum causes sheet deformation.
Features of Slalom-Configured Roll-to-Roll Furnaces Using Wavelength-Control Heaters
Replacing vacuum batch drying furnaces with NGK slalom-configured roll-to-roll furnaces incorporating wavelength-control heaters offers the following advantages:
(1)Allows continuous dehydration (absolute drying).
The dehydration (absolute drying) process is performed continuously for each roll. This provides the following benefits:
- Eliminates the need for roll form drying space.
- Eliminates the need for drying chamber temperature/humidity control.
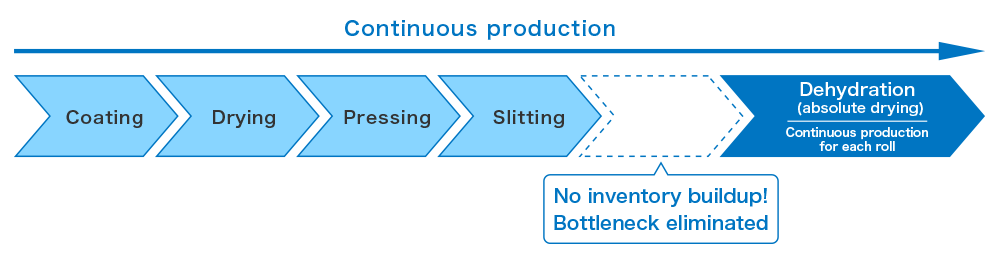
(2)Enables sheet form dehydration (absolute drying).
Dehydration is possible in sheet form in the dehydration (absolute drying) process. Sheet form drying provides the following benefits:
- Cuts the processing time required to achieve complete dehydration (absolute drying), improving productivity.
- Eliminates overlapping of the sheets for uniform drying.
- Sheets do not deform.
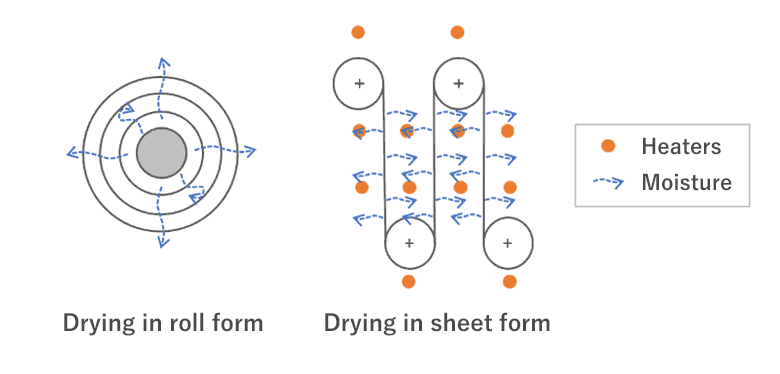
(3)Allows dehydration (absolute drying) at low temperatures.
The wavelength-control heater incorporates the world’s first technology that allows selective emission of infrared radiation at the wavelengths absorbed by the solvent, allowing solvent drying without raising the temperature of the coating layer or substrate.
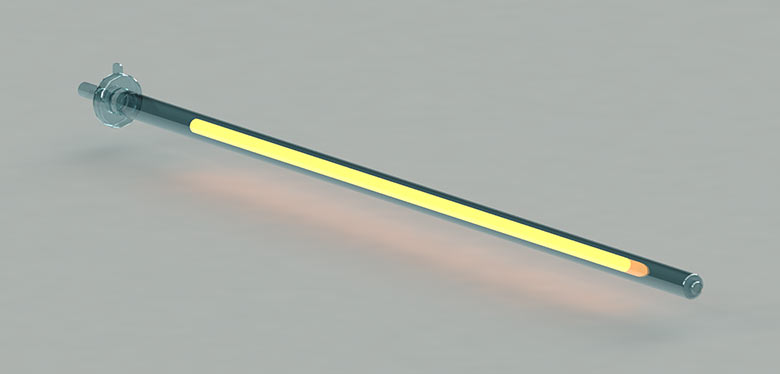
(4)Energy savings and CO2 reductions
A drying chamber is no longer required for rolls, halving the amount of dry air needed and helping to reduce energy consumption and CO2 emissions.
(5)Space savings
The slalom-configured roll-to-roll furnace (patented) is more compact than conventional straight-configured roll-to-roll furnaces. This saves still more space beyond the process space saved by eliminating the roll drying chamber.
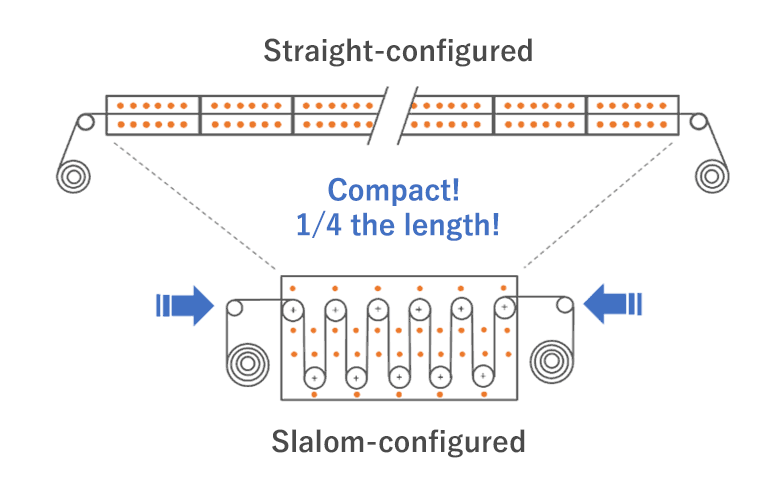
Summary of Features
Item | Vacuum batch type | Slalom-configured roll-to-roll furnace incorporating wavelength-control heaters | Remarks |
---|---|---|---|
Productivity | Poor due to batch system | Continuous production for each roll | Eliminates the need for vacuum and drying chamber; eliminates inventory buildup awaiting dehydration (absolute drying). |
Dehydration time/temperature | Approx. 1 day | Approx. 10 mins | Cuts dehydration times to less than 1/100, even at the same dehydration temperature. |
Dehydration (absolute drying) performance | Approx. 1,000 ppm | Approx. 200 to 600 ppm | Improves dehydration (absolute drying) performance. |
Substrate dehydration variations | Susceptible | Does not occur | Dehydrates substrate (absolutely dry) while spread out, eliminating dehydration variations. |
Substrate deformation | Susceptible | Does not occur | Dehydrates lithium-ion battery electrode substrate (absolutely dry) at normal pressure, eliminating deformation. |
Energy savings/CO2 reductions | - | More energy efficient than vacuum batch system | Eliminating the roll drying chamber cuts dry air volumes by more than half. |
Space savings | - | Space savings compared to vacuum batch system | Requires less than half the space taken by a vacuum batch furnace; eliminates the need for drying chamber space. |
Test Facility
NGK provides a slalom-configured roll-to-roll furnace incorporating wavelength-control heaters for test purposes to allow customers to perform test drying using actual production conditions before purchasing. This allows testing under a wide range of conditions while adjusting parameters such as dew point, feed speed, furnace internal gas flow rate, and heater output to suit individual film and substrate coatings (solvent type, thickness, initial moisture content) and requirements and restrictions, such as temperature resistance.
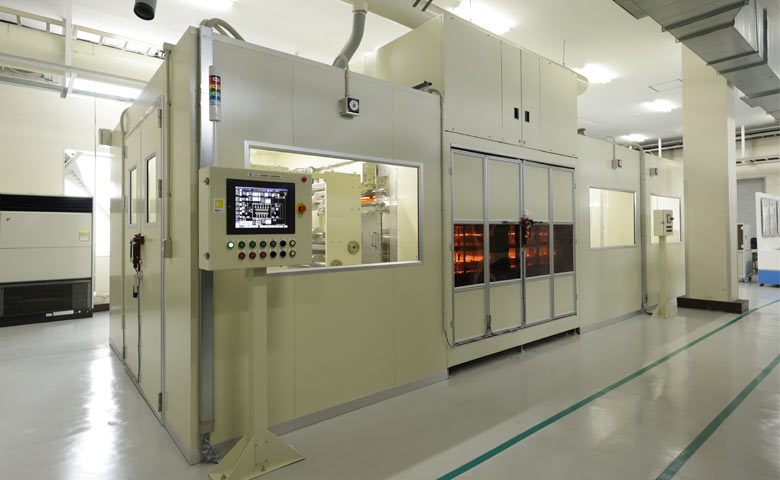
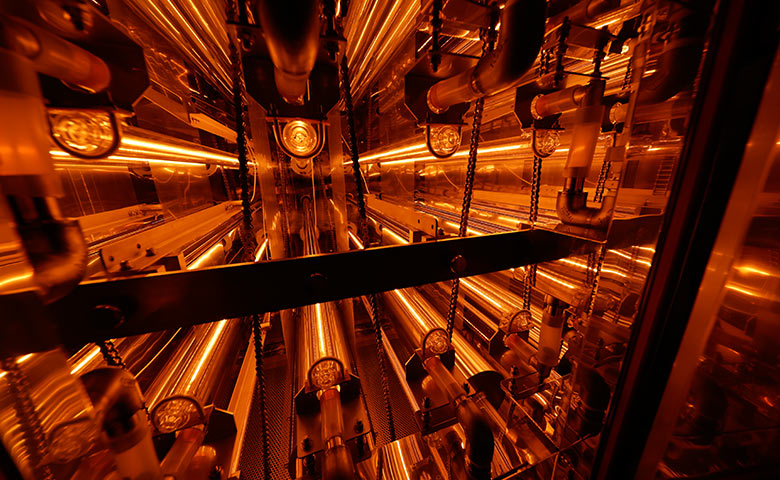
Test Facility Specifications
Item | Specifications |
---|---|
Film/substrate width | Max. 700 mm |
Film/substrate length (in-out) | 13.2 m |
Film/substrate thickness | 100 to 200 µm |
Roll diameter | Max. 400 mm |
Core | 3-inch or 6-inch (adapter compatible) |
Feed speed | 10 to 200 m/min |
Tension control | Normal: 50 to 150 N (supported range: 10 to 200 N) |
Furnace internal temperature | Normal: 80 to 200 °C (supported range: 50 to 250 °C) |
Cleanliness level | 10,000 |
Atmosphere | Atmospheric air, dry atmosphere (atmospheric air, dew point -40 °C) |
Heaters | 33 sets, with individual variable output control (max. 120 kW) |
Utilities | Electricity: 200 V, 3-phase, 600AT/600AF Supply/exhaust: 10 Nm3/min *Also compatible with 380 V. |
Inquiry about Industrial Heating Systems
Please apply with the contact form and give us your comments or questions.