Scaling up direct air capture for a net zero future
This content was paid for by NGK Insulators and produced in partnership with the Financial Times Commercial department.
The science is clear.
If we want to stabilise the climate, we can’t just reduce emissions; we must also remove vast amounts of carbon dioxide accumulated in the atmosphere. Meeting Paris Agreement goals will require gigatonnes of carbon to be effectively scrubbed out of the ambient air. This means restoring natural ecosystems that can act as carbon sinks and deploying various carbon removal technologies.
One promising solution is direct air capture (or DAC), a technology that removes carbon directly from the ambient air through a chemical process.
A 2020 World Resources Institute report finds DAC has key advantages over afforestation and reforestation, the major strategies for removing atmospheric carbon. DAC requires relatively less land and water than planting trees, and can be sited in areas unsuitable for growing forests, such as deserts and colder climates. And CO2 captured by DAC, when stored geologically, provides a more permanent and assured quantification of carbon removal than when done through afforestation. If not stored, it can be used as a climate-neutral resource for products like chemicals, synthetic fuels, and carbonated beverages.
Once a costly fantasy, DAC is morphing into reality, with governments, industries and investors rallying behind the technology. As of 2023, the US - leading the charge - has announced a gargantuan USD 3.5bn in government grants for plants which will capture and permanently remove carbon from the atmosphere.
According to the International Energy Agency (IEA) latest report from July 2023, 18 DAC facilities are operating worldwide. The largest facility today is in Iceland and is powered by geothermal energy. It extracts up to 4,000 tonnes of CO2 annually (tCO2/y), sending it deep underground after mixing with water to eventually turn into rock. New DAC sites are being announced, including one in Texas that is under construction and expected to be up and ready by mid-2025 capable of capturing up to 500,000 tonnes of CO2 every year.
Challenges of scaling up DAC
To make material impact, DAC must be scaled up fast. The IEA estimates that an average of 32 large-scale plants, each capable of capturing 1 megatonne of CO2 per year, need to be built annually between now and 2050. Total annual capacity will have to hit 0.98 gigatonnes by then, roughly 100,000 times more than it is today.
The key bottleneck to setting up a vast DAC system is cost. Greenhouse gases, including CO2, are much less concentrated in the ambient air from which DAC captures them than that coming out of factory or power plant flues. As such, it requires significant amounts of energy to extract.
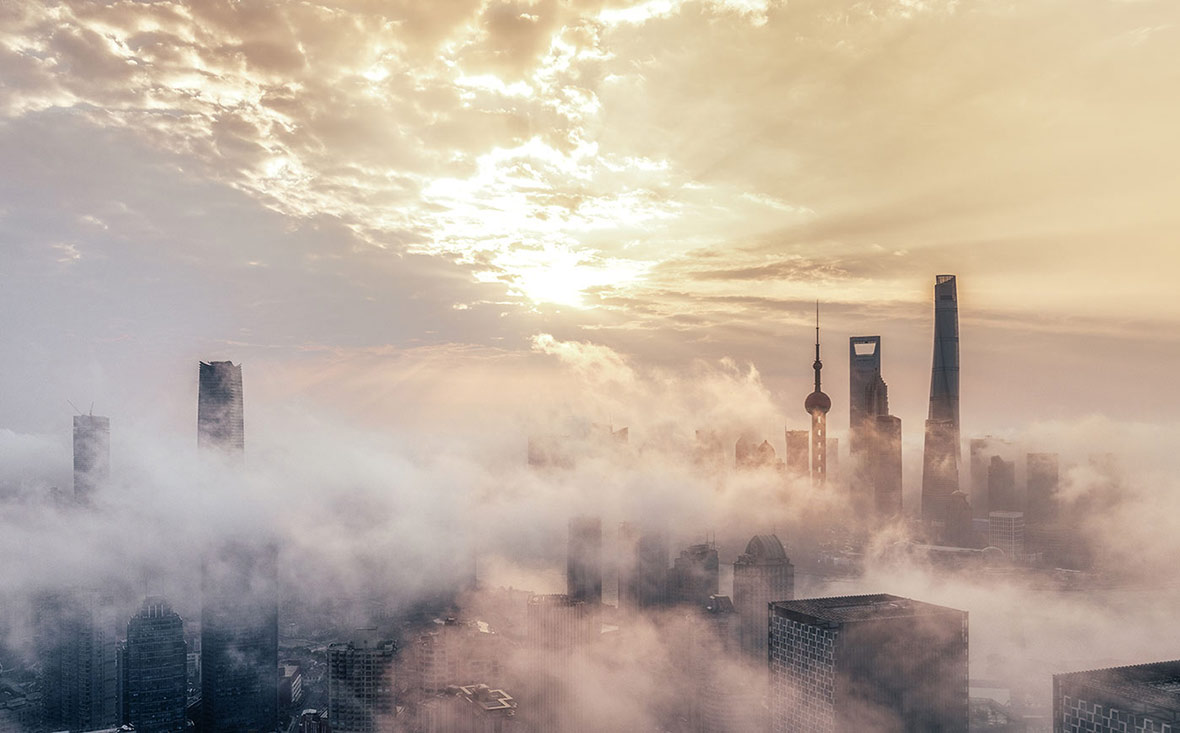
And for DAC to make sense, energy used in the process must come from low-cost and low-carbon sources to ensure economic feasibility and negative emissions. The IEA estimates that locations with large amounts of cheap renewable energy – such as giant desert solar farms – using the best available technologies for electricity and heat generation will help lower costs of DAC to below USD 100 /tCO2 by 2030, compared to USD 600 at current levels.
Another factor influencing the cost of DAC is the type of technology used. There are several competing technologies, including the leading “solid sorbent” process that draws in ambient air with fans and passes it over chemicals that selectively bind to CO2. The trapped CO2 is then later released and collected in concentrated form for storage or usage.
These “solid sorbent” plants currently in operation employ fibre or pellets coated with sorbents such as amines to capture the CO2. Replacing those pellets with ceramic-based honeycomb structures could generate considerable efficiency savings in energy and lower costs.
Why ceramics for DAC?
NGK Insulators Ltd., a Japanese ceramic technology company, believes that its honeycombed-structured substrate — which it has supplied for decades as catalytic converters to purify exhaust gases from car combustion — is suitable for DAC.
“We believe that the honeycomb structure with ultrathin walls, providing a very large surface area, has the advantages of less pressure loss and low heating capacity,” explains Shigeru Kobayashi, NGK’s president. “This means we expect less electricity needed for pushing the air through the contactor and heat for releasing the captured CO2, making it more efficient than existing approaches.”
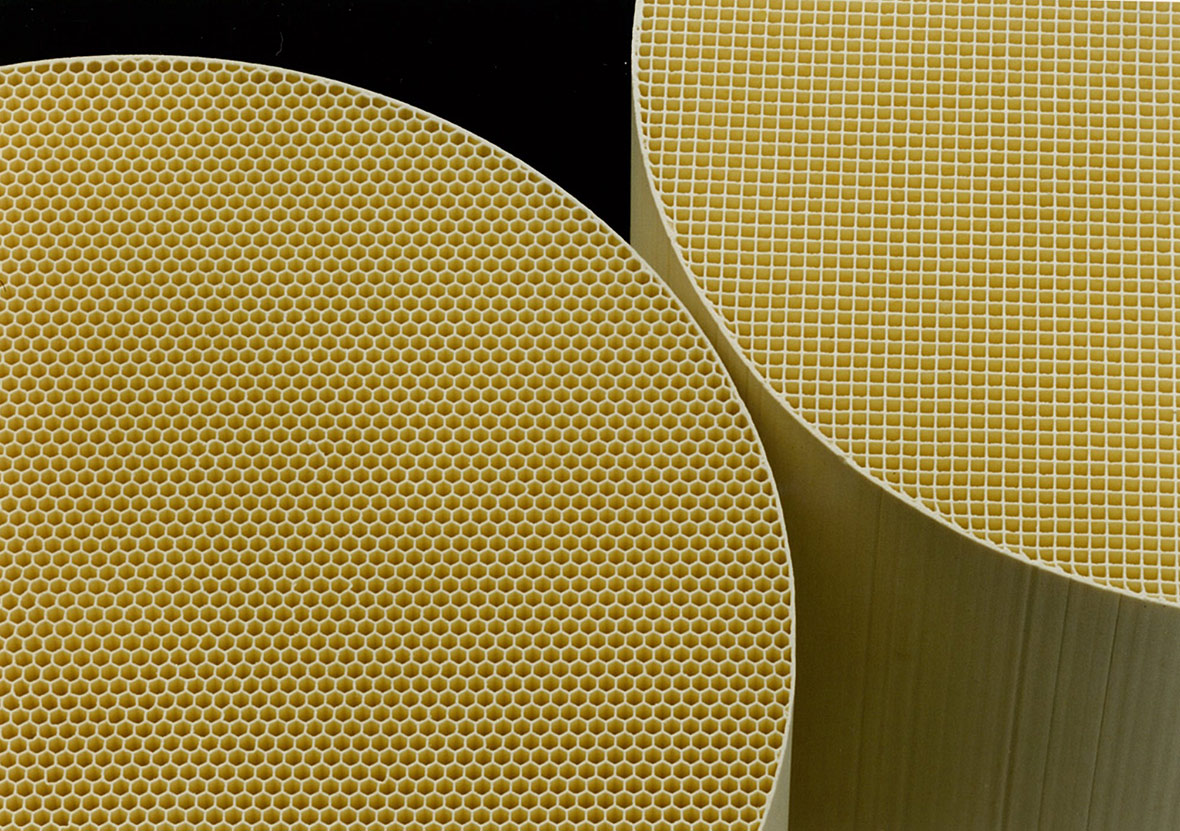
Ceramics are also highly durable and are expected to offer more structural stability, longer lifespans and lower capital costs than nanofibers.
“Besides us, another global manufacturer is developing ceramic components for DAC use, but we hope to differentiate through the type of support layer used and its combination with different CO2 sorbents,” says Kobayashi.
An equally important part of the strategy is that NGK and others have established highly efficient production lines and supply chains to mass produce these substrates for the millions of automotives produced annually.
The calculations are compelling.
NGK’s 12 factories worldwide produce several hundred million litres per year of honeycomb ceramics used to purify car exhaust. The company expects that 30 litres of ceramics are needed to extract one tonne of CO2 annually. NGK aims to modify its existing plants to supply a significant portion of the 300 million litres of honeycomb required when DAC is scaled up to achieve the carbon removal necessary to reach climate targets.1
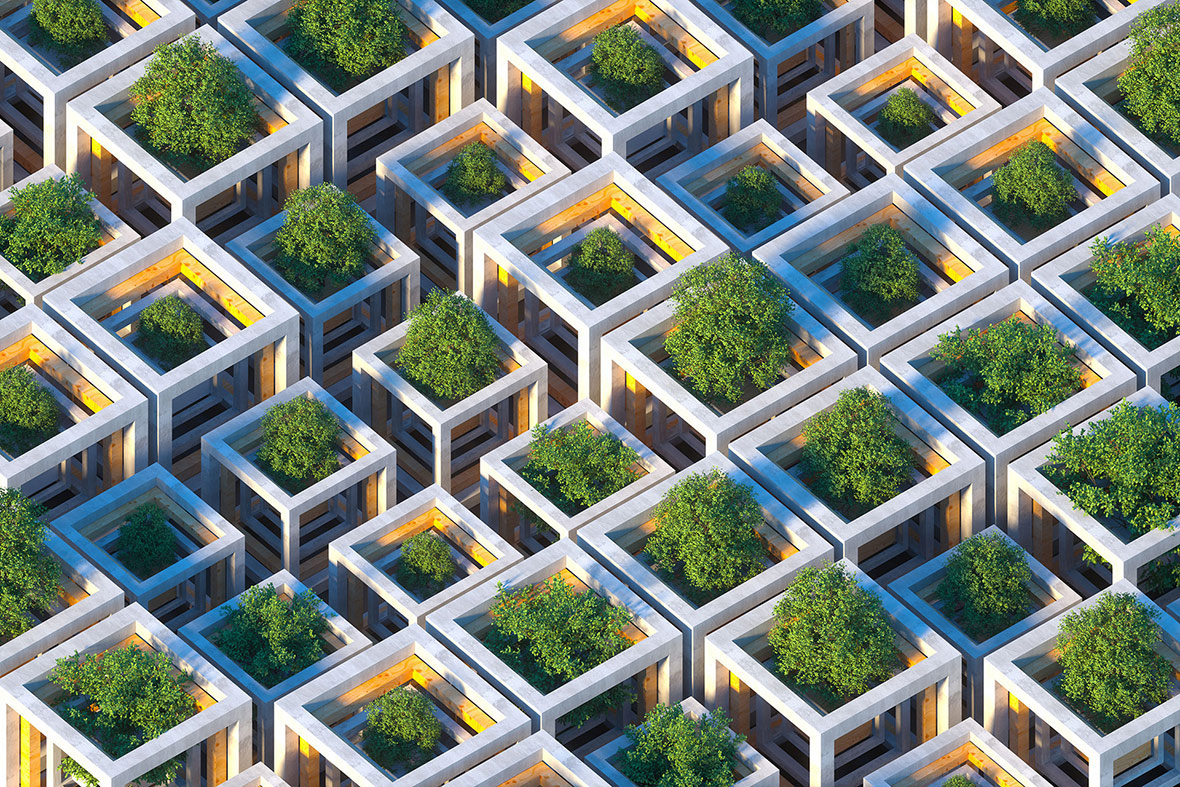
“We believe that our honeycomb production lines can be converted relatively easily to mass produce these DAC components”, says Kobayashi. Currently, the company is supplying samples and aiming to achieve demonstration tests by 2025.
The company’s initiative to supply ceramic components for direct air capture is one of many ceramic-based solutions NGK hopes to provide for a decarbonised future.
Other solutions on the table include NGK’s unique grid-scale storage battery to contribute to renewable energy storage; subnano-ceramic membranes to filter materials at a molecular level, including carbon dioxide for various carbon capture use and storage (CCUS) applications; as well as ultra-thin batteries to enable maintenance-free IoT devices.
NGK says its broader vision is to “realise things which were previously considered technically infeasible”. Such an approach will be needed to reverse centuries of emissions and stabilise climate change.