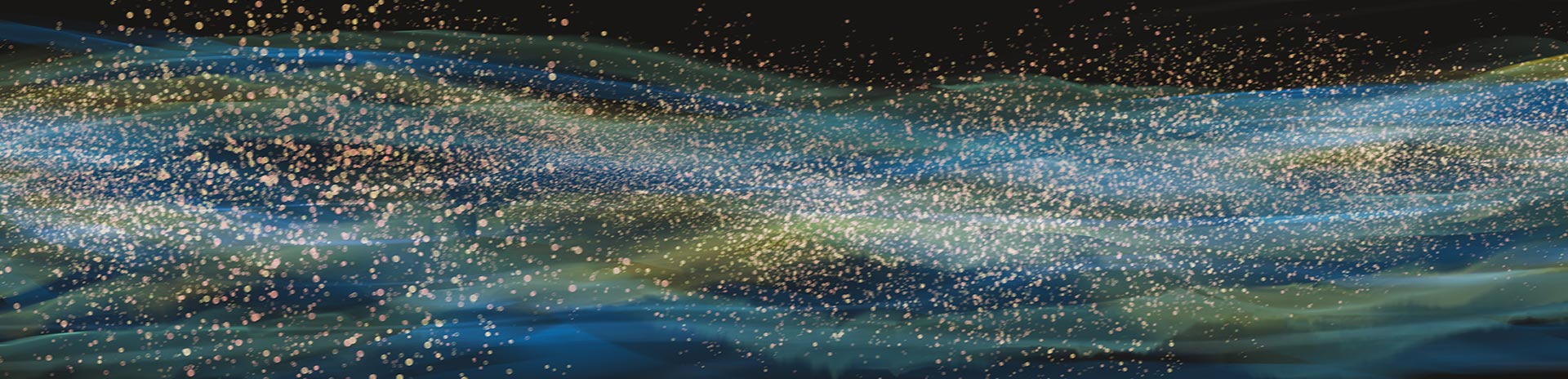
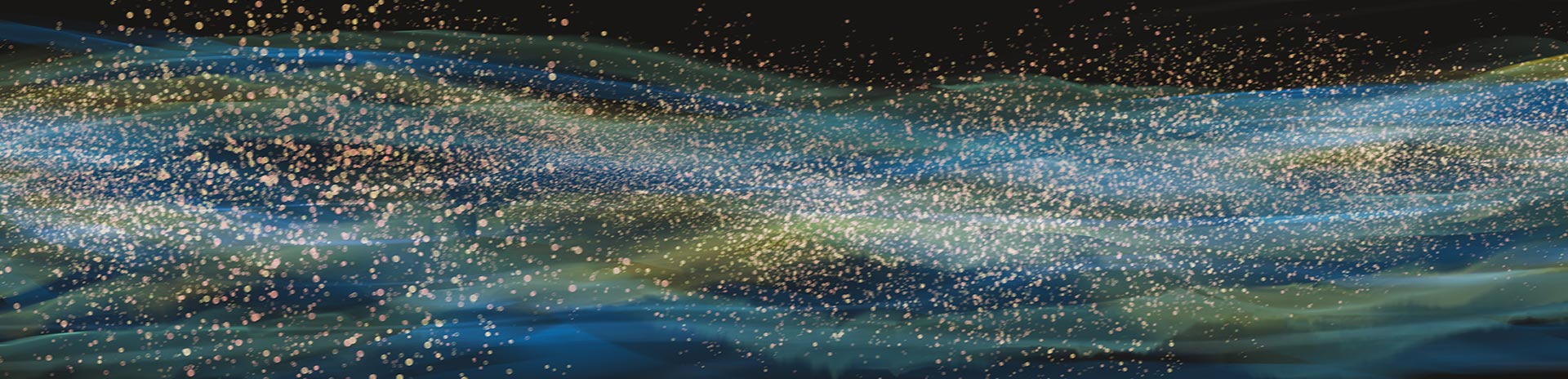
Creating new products
“Sub-nano Ceramic Membrane” Capable of Molecular Separation
What are Separation Membranes?
The various technologies used to separate substances include distillation, crystallization, extraction, and filtration. Among these technologies, membranes that are used to separate substances via filtering are called separation membranes. Separation membranes are broadly classified into ceramic, organic, and carbon types.
What are Sub-nano Ceramic Membranes?
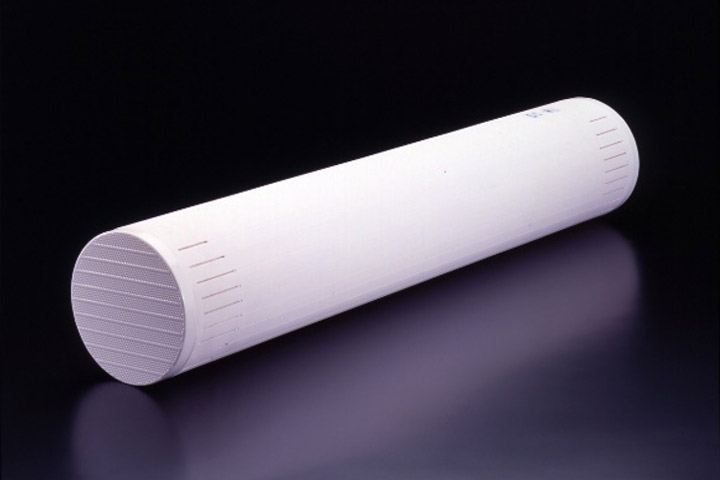
Sub-nano ceramic membranes are ceramic separation membranes (ceramic filters) that feature especially fine sub-nano* class pores. They are capable of separation at the molecular level – for example, separating nitrogen from a mixed gas of methane (CH4) and nitrogen (N2).
NGK has developed various sub-nano ceramic membranes capable of separating specific gases or liquids from gas-liquid mixtures. These products are instrumental to establishing innovative separation processes that dramatically reduce both costs and energy consumption.
* Sub-nano: less than 1 nm (nanometer); 1 nm = 0.000001 mm.
Types of Ceramic Membranes and Scope of Application
NGK offers optimal filtration solutions based on a wide lineup of products, ranging from dust collection systems for industrial exhaust gas to low molecular separation systems for pharmaceutical manufacturing processes.
Sub-nano ceramic membranes are characterized by exceptionally small pore size, which enables molecular separation. As one example, these membranes can be used to isolate CO2 from a gas mixture, a function that contributes significantly to carbon neutrality.
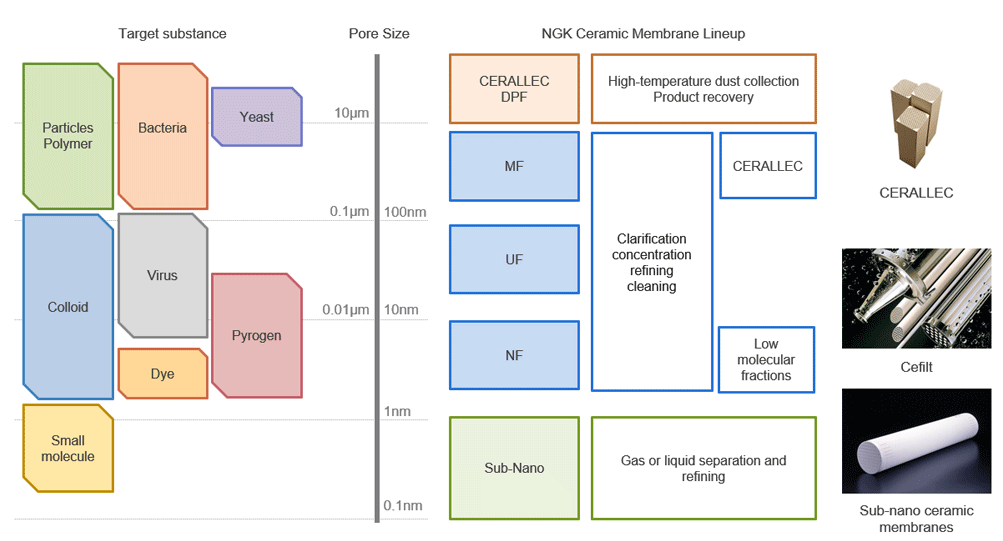
Features of Sub-nano Ceramic Membranes
Sub-nano ceramic membranes have the following features not found in organic and carbon membranes used in conventional membrane separation technologies:
(1) Capacity to perform molecular separation
These membranes achieve molecular separation of gases and liquids via a layer of zeolite or other materials, which has molecular-scale pores and covers the cell surface.
(2) Uniform pore size for high separation performance
NGK’s sub-nano ceramic membranes use crystalline zeolite or other materials, which has uniform fine pores, for the separation layer, thereby achieving high separation coefficient compared to organic membranes and carbon membranes used in conventional membrane separation.
These sub-nano ceramic membranes also allow selection of the separation layer type based on the target molecule, thereby enabling the separation of a wide range of molecules.
For example, DDR-type zeolite, composing the separation layer of DDR-type zeolite membranes, is a crystalline material characterized by oval pores with 0.36 nm × 0.44 nm. The minor axis of the pore (0.36 nm) is longer than a CO2 molecule (0.33 nm) but shorter than a CH4 molecule (0.38 nm). When a CO2-CH4 gas mixture is supplied to the DDR-type zeolite membrane, CO2 molecules will permeate preferentially to achieve high separation coefficient.
Size of zeolite pores and molecules
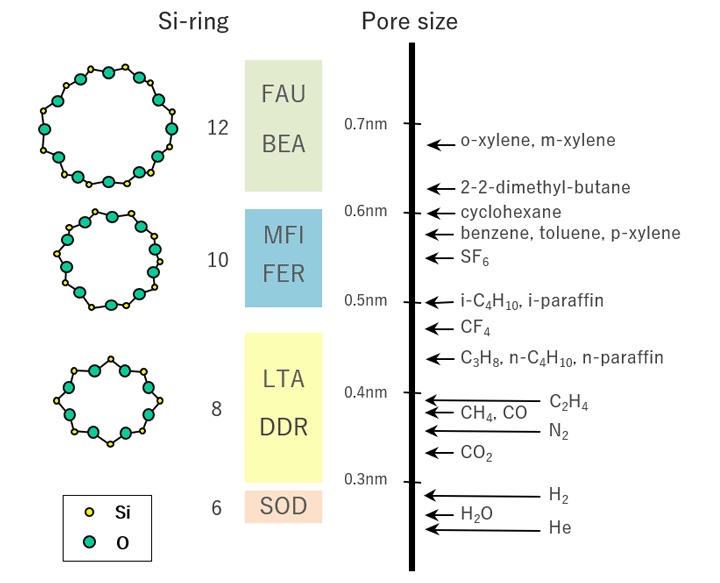
Molecule separation image using DDR-type zeolite membrane
Conventional membrane
Ununiform pores
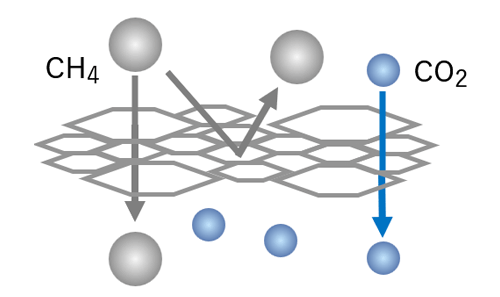
DDR-type zeolite membrane
Uniform pores based on crystal structure
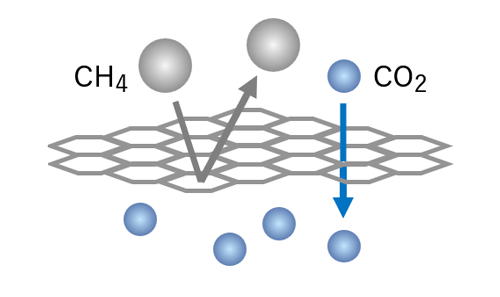
Single gas permeance of DDR-type zeolite membrane
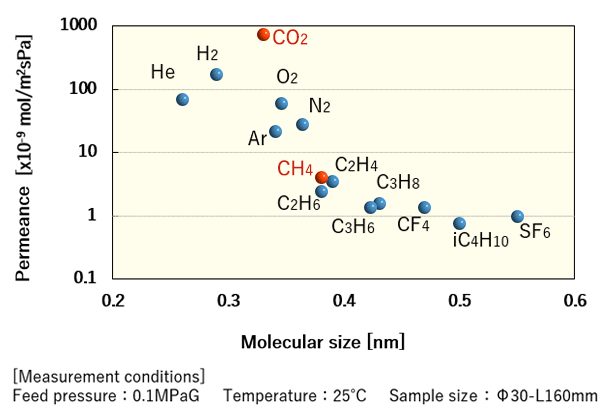
(3) Realizing more compact and energy-saving separation systems
Methods like amine absorption for CO2 separation, cryogenic separation for N2, and distillation for organic liquid dehydration offer high separation performance but require huge equipment and consume significant amounts of energy. Use of NGK’s sub-nano ceramic membranes can eliminate the need for energy-intensive heating processes for these processes, thereby saving energy, reducing CO2 emissions, and enabling to downsize your facilities.
(4) High heat resistance, pressure resistance, and durability
As they are made of ceramic materials, NGK’s sub-nano ceramic membranes offer excellent heat resistance and pressure resistance, making them ideal for use with various gases and liquids across a wide range of temperatures. Due to the high mechanical strength and rigidity of ceramics, membrane structures undergo minimal deformation even when exposed to pressure and heat, thus offer long service life.
(5) Reduced pressure loss and high permeability
The base material on which the separation layer is formed has a multilayer structure consisting of a surface layer and a support layer featuring arrangements of pores of different sizes. Compared to a single-layered structure with uniform pore size throughout the base material, the multilayer structure can greatly reduce pressure loss. We can achieve high permeability by forming a separation layer on such base materials with multilayer structure.
(6) Large membrane surface area for high processing capacity
The honeycomb structure created by the approximately 1,600 cells penetrating lengthwise through a columnar ceramic base material measuring 180 mm in diameter and 1,000 mm in total length results in high processing capacity. Unlike membrane tube products that need to be bundled together to create a module, NGK’s sub-nano ceramic membranes require fewer parts, resulting in more compact equipment and cost reduction.
Structure of a Sub-nano Ceramic Membrane
Molecular separation is achieved by forming a dense separation layer made of zeolite or other materials, which has fine pores of less than one nanometer (one billionth of a meter) in diameter, on the inner surfaces of approximately 1,600 cells penetrating lengthwise through a columnar porous ceramic base material measuring 180 mm in diameter and 1,000 mm in total length. By switching the separation layer type according to the target substance, we can control pore size to selectively separate desired molecules.
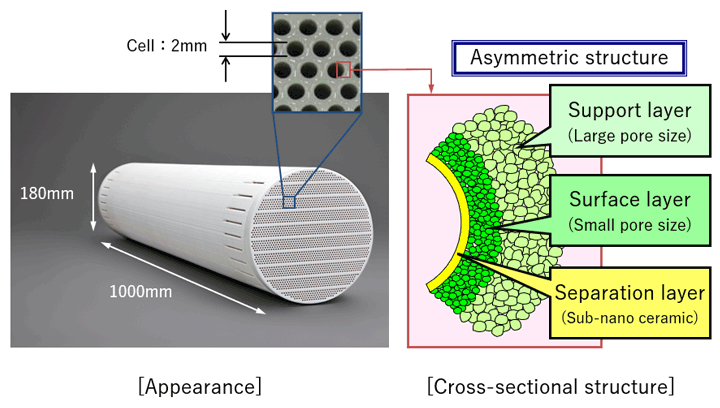
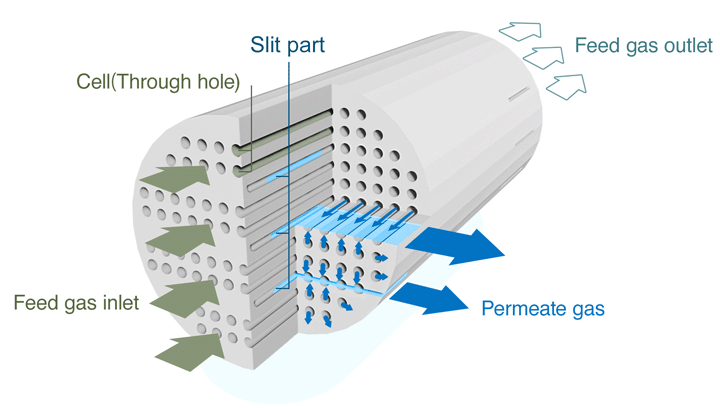
NGK’s sub-nano ceramic membranes separate specific molecules based on differences in molecular size and adsorption properties. Suppose we use NGK’s sub-nano ceramic membrane to separate a gas mixture containing molecules larger and smaller than the pores of the separation layer. Since only molecules smaller than the pores can pass, we can efficiently isolate a gas characterized by small molecules from a gas characterized by large molecules.
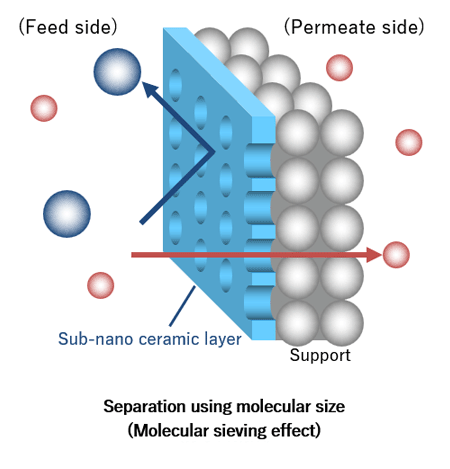
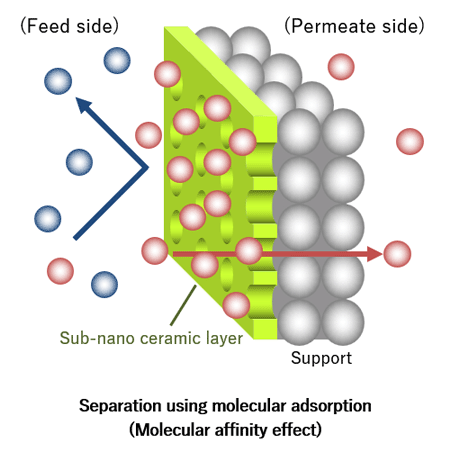
Related Products
NGK offers a wide range of ceramic filter products with different pore sizes.
Featured Articles
Inquiry about Research & Developments
Please apply with the contact form and give us your comments or questions.