Sustainability
Occupational Safety and Health
Basic Approach
The NGK Group operates an ISO 45001-certified Occupational Safety and Health Management System (OSHMS) in line with its Safety and Health Policy. The OSHMS serves as a mechanism for the ongoing, systematic achievement of worker safety and health initiatives. By strictly implementing this system and conducting risk assessment-based safety measures, we strive to raise the level of occupational safety and health throughout the entire Group, including for contractors on-premises.
Structure to Promote Safety and Health Management
NGK established the Environment, Safety and Health Committee chaired by the Managing Executive Officer who is the person in charge of safety and health in order to raise the level of the entire Group’s safety and health. This committee meets at least biannually to deliberate and determine the Group’s initiatives and action plan as well as monitor the results of activities, situation of work-related accidents and countermeasures. The committee reports to the Board of Directors which also monitors its activities. Moreover, every business site holds Business Site-Specific Safety and Health Committee meetings monthly led by relevant labor representatives of every department and attended by General Safety and Health Manager (directors of each site/vice presidents). In addition to promoting awareness of Group activities and action plans, the committees investigate and deliberate important matters related to safety and health unique to each business site, and then penetrate and implement findings through the Safety and Health Committee members of each workplace.
Safety and Health Management Organizational Chart
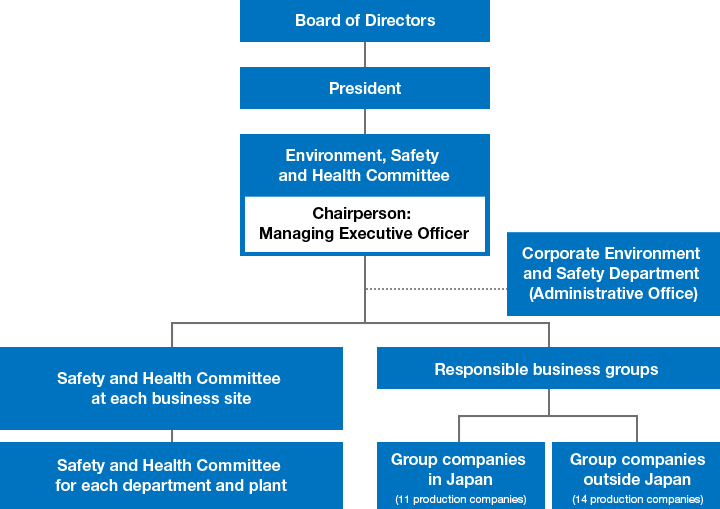
Enhancing Safety and Health Activities
NGK views the enhancement of safety and health activities as one of its top priorities. In addition to rigorous operation of our occupational safety and health management system, we developed our third three-year action plan to start from FY2023. It is built around the key themes of compliance, governance, and risk reduction. We are promoting safety and health activities with our action policies defined as ensuring thorough legal compliance, further enhancing our Group governance structure, and preventing serious accidents and disasters. Concerning preventing serious accidents and disasters, in addition to comprehensive risk assessments covering existing facilities and operations, when introducing new facilities or operations or modifying operations, we conduct a thorough risk assessment in advance to eliminate risks or reduce them to an acceptable level. All of NGK’s business locations and plants as well as manufacturing Group companies in Japan and overseas have obtained ISO 45001 certification.
Results of FY2023 Activities
Medium-Term Action Plan | Fiscal year implementation items | Key Activities |
---|---|---|
Compliance | Strengthen mechanisms for compliance with laws and regulations | We carried out training for managers/representatives, in addition to conducting general surveys and corrective action at all business units including Group companies concerning compliance with laws and regulations related to safety and health. Moreover, we have put internal regulations in place to prevent non-compliance with laws and regulations, such as failure to report to the government. At the same time, we have begun to build a database that will allow us to respond to all legal requirements related to safety and health. |
Group Governance | Strengthen safety and health functions in each business group | We have clarified the division of roles between the department which oversees safety and health at the head office, and the safety and health departments in each business group. We are now setting up an autonomous structure that enables the safety and health departments at each business group to manage/promote safety and health at factories and group companies under their jurisdiction. |
Risk reduction | Reduce the risk of serious accidents or injuries | We comprehensively extracted and identified high severity risks related to getting caught and entangled in rotating machinery, electric shock and explosion. Not only did we implement operational solutions for curtailing risks (administrative measures), but also completed equipment countermeasures (upgrades and modifications) except for at some of our locations outside of Japan. We have also established various internal regulations related to safety management. |
Numerical Targets
NGK has set the following numerical targets for 2024.
- Zero fatal or serious accidents throughout the Group
- Group-wide lost-worktime accident severity rate of 0.01 or less
In 2023, we achieved zero fatal or serious accidents throughout the Group. Additionally, the group-wide lost-worktime accident severity rate was 0.010, meeting our target value of 0.01 or less.
Work-Related Fatalities
Work-Related Accidents
Trends in Work-Related Accidents
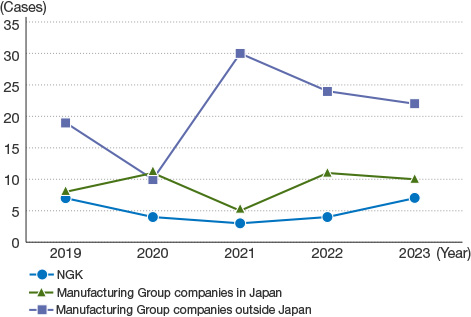
Work-Related Accidents by Type (past 7 years; NGK Group consolidated)
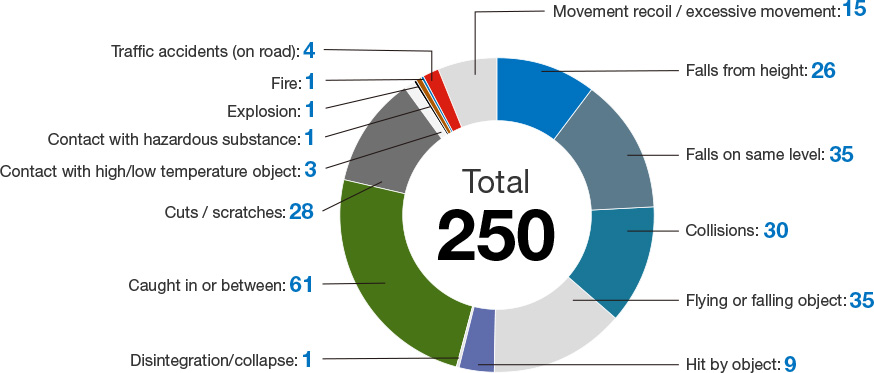
Response to Work-Related Accidents
In the event of a work-related accident, following the NGK Group’s rules, we promptly notify relevant departments and convene the Work-Related Accident Deliberation Committee pursuant to the regulations of each company. This ensures that we are able to thoroughly identify the cause and implement countermeasures against future recurrence.
In 2023, there were 39 non-lost worktime and lost worktime accidents Groupwide. Broken down, these included seven at NGK, 10 at manufacturing Group companies in Japan, and 22 at manufacturing Group companies outside Japan. The number of times employees were caught in rotating machinery (which was something we addressed as a priority activity) was 2, and both victims were severely injured. These accidents occurred due to a failure to conduct thorough risk assessments of the work and to uncover serious hidden risks. Therefore, we have begun new training for personnel in charge of manufacturing sites which aims to strengthen their ability to discover potential hazards during risk assessments.
Number of Contractor Accidents Severe Enough to Result in Lost Worktime
Number of Contractor Deaths
Severity Rate (Number of Lost Workdays per 1,000 Hours Worked)
Lost Time Injury Frequency Rate (Employees)
Occupational Illness Frequency Rate
External Certification of Occupational Safety and Health Management System
To continuously raise the level of occupational safety and health in workplaces, we encourage companies in the NGK Group to acquire international certification for occupational safety and health management systems.
In 2017, NGK’s Nagoya Site received the first ISO 45001 private certification in Japan. In 2018, all other NGK sites and plants in Japan received ISO 45001 certification and JIS Q 45100 certification.
As of June 2021, all 26 manufacturing Group companies in Japan and overseas have completed the acquisition of ISO 45001.
Acquisition of Occupational Safety and Health Management System Certification
Safety and Health Training
NGK provides training to employees and assists with their acquisition of qualifications/licenses required under safety and health laws and regulations. Our training includes various in-house programs on safety and health along with curriculum sourced from outside NGK. In FY2023, a total of 3,842 employees received in-house group training on safety and health standards. The breakdown includes rank-based training/training for newly-promoted employees (671), danger prediction training (3,104), and ISO 45001 internal audit training (67). This excludes training conducted by each department such as worker training, job rotation training and risk assessment training, external training for crane operators and the like, and safety officer training.
Main Training Programs
Training programs | Training curriculum |
---|---|
Legal training | Group training mainly for managers through videos that provide a summary of safety and health related laws and regulations |
Internal safety and health training | In-house group training required of employees, including training on dust, KYT (hazard prediction training), risk assessment, etc. |
External safety and health training | Training conducted offsite required of employees, including for workplace supervisors, low-voltage electricity, organic solvents, Video Display Terminal (VDT), lift/crane operators and various operation chiefs |
New employee training | Group training for new graduate hires and individual training provided to newly assigned employees including temporary employees |
Job rotation training | Training conducted by each department for employee transfers and work changes |
Stratified education /Promotion training | Training provided at the time of promotion, including new promotions as well as newly appointed assistant managers, managers, general managers, and directors of business sites Stratified education training is provided to new graduate hires, mid-career hires, and workers promoted to regular employee status |
Internal auditor training | Group training for the purpose of developing and improving the level of ISO 45001 internal auditors |
Worker training | Training and exercises for frontline work are conducted to evaluate skill level and certification of work proficiency |
Frontline management training (safety officers) | (See below) |
Danger-Prediction Training Center | (See below) |
Acquisition of Safety Officer Qualification
To increase their managerial skills, we train managers to become Safety Officers through e-learning and encourage them to obtain Safety Officer Qualification*. As of FY2023, 447 managers in research & development and engineering departments, including general managers, plant managers, and managers of the manufacturing department had obtained this qualification. We also encourage engineers of design and maintenance departments for in-house equipment and production engineers at our plants to obtain Safety Assessor Qualification*.
Safety Officer Qualification / Safety Assessor Qualification: Qualifications established and administered by The Institute of Global Safety Promotion (IGSAP). The qualifications certify that an individual possesses understanding and knowledge of safety or knowledge and skills of machinery based on international safety standards, respectively.
Establishment of Danger-Prediction Training Center
To prevent injuries mainly among young workers and inexperienced workers, in 2018 we established the 450 m2 Danger-Prediction Training Center at our Chita Site, where we launched safety training led by specialist employees with experience outside of NGK.
The training center features equipment that enables employees to safely experience work-related injuries that have occurred in the past including caught in rotating machinery or in equipment and work-related accidents that could lead to serious injury such as electric shock or explosions. Combined with classroom learning using computer graphics, the training center provides practical programs where employees can refine their sensitivities toward dangers.
In 2020, we introduced a virtual reality system for experiencing dangers and conducted a training program that combines this with conventional training approaches. This training was rolled out to Group companies in Japan as well, and as of FY2023, a running total of 9,431 NGK Group employees have participated.
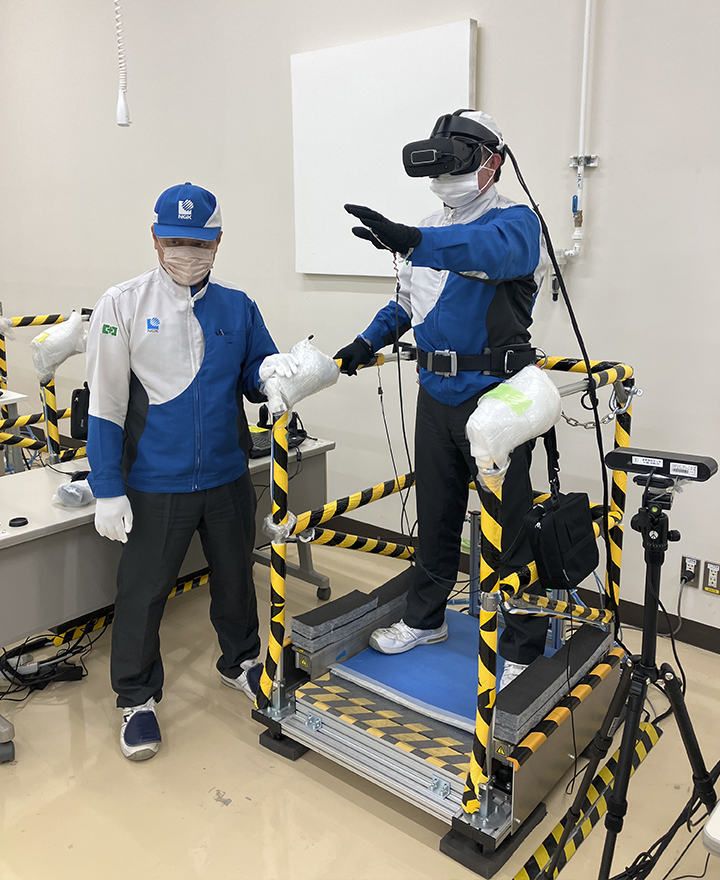