Sustainability
Pursuing Quality for Products and Services
Basic Approach
Guided by the Corporate Philosophy, which puts customers first, the NGK Group considers the provision of products and services that contribute to a better social environment to be one of its most important missions in attempting to create quality from the customer’s perspective.
The NGK Group defines Quality Objectives each year in accordance with the Quality Policy based on the NGK Group Corporate Business Principles. This policy is focused on working to improve the quality of our operations* and reduce quality risks as our primary activities to increase customer trust. Moreover, we enhance our activities to increase customer trust by carrying them out in tandem with quality improvement activities.
Quality of operation: Level of operational systems that are in place to ensure that promises made to customers are fulfilled.
Quality Objectives FY2024
Everyone from management to workers in the field thoroughly discusses overburden, waste, and unevenness in our operations, and works to improve them.
Quality Activity System
The NGK Group quality activity system consists of a company-wide system, led by the Quality Committee Chair (Executive Vice President), and business division internal activity systems, led by the heads of each business group. In terms of company-wide activities, the Quality Committee was established to function as a deliberative body assisting the Quality Committee Chair, while business division internal activity systems were put in place for each business division, creating appropriate quality systems for each. Quality assurance, quality control, quality improvements, and quality education activities are promoted by the acquisition of ISO 9001 or IATF 16949 certification.
Each business group maintains a point of contact with customers, and works to further increase customer satisfaction by reflecting customer demands and things learned from quality problems in the market in our products and services.
Quality Activity System
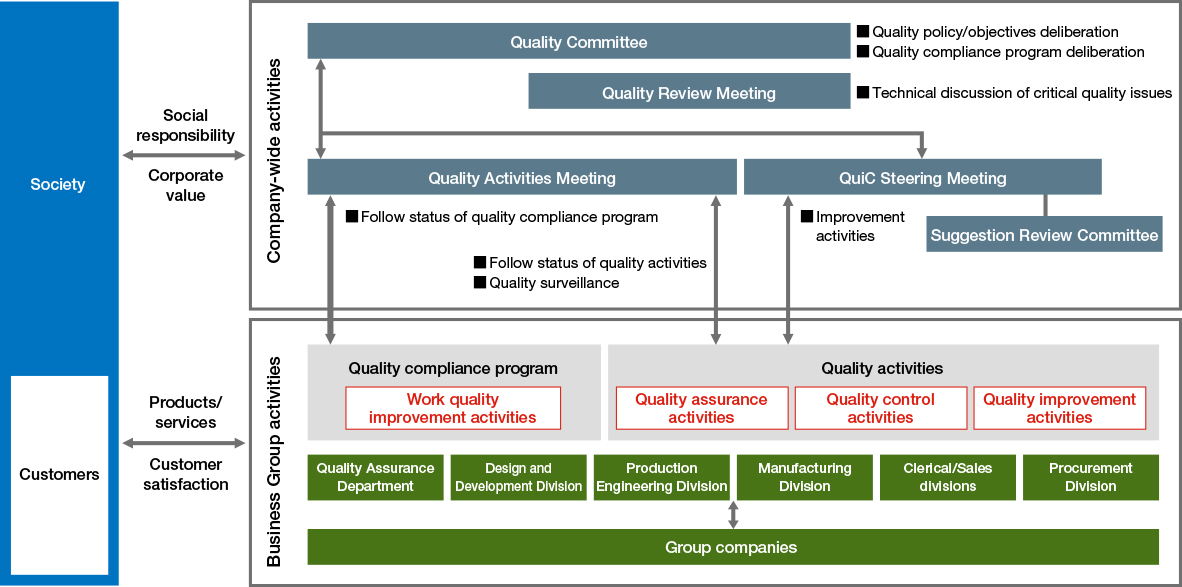
Quality Control Systems Outside Japan
From their inception, production bases outside Japan have created quality systems appropriate to their situations and acquired ISO 9001 or IATF 16949 certification.
Monthly reports from each base regarding customer complaints and the status of manufacturing quality are discussed at Quality Activity Meetings, enabling the entire NGK Group to evaluate the quality status in a timely manner. Moreover, quality activity rules and annual quality objectives are distributed group-wide in an attempt to develop and enhance quality activities.
Acquisition of ISO 9001 or IATF 16949 Certification
NGK and the all business group production sites, supporting functions, and locations at Group companies in and outside Japan have acquired ISO 9001 or IATF 16949 certification.
Activities to Increase Customer Trust
Improving Quality of Operations
Since FY2021, the initiative to improve "quality of operation" that we started in FY2018 has aimed to get each employee in the workplace to autonomously improve the quality of their work. As these efforts proceed, we are starting to form an organizational culture of being open about problems. In FY2023, as in FY2022, we continued to work on each initiative in our company-wide quality compliance program. These include declarations of intent from management, establishing rules and regulations, conducting training, audits and monitoring, and preventative activities. Thanks to our efforts to prevent overburden and ambiguity in operations and ensure thorough communication, we have reviewed workloads and work rules, and are making progress on the understanding and dissemination of quality compliance in our workplaces and the front lines of operations at Group companies.
In FY2024 we are further enlarging the scope of our activities, and strengthening activities that ensure everyone from management to the front lines takes ownership of quality compliance and engages in discussions about the quality of operations to promote understanding.
Reducing Quality Risks
4 Rules for Quality Activities
The NGK Group promotes restructuring of its quality activities to respond more precisely to increasing and diversifying quality demands from customers in different target markets. We have formulated these quality activity rules particularly to enhance the elimination of quality risks in the market, and are promoting their adoption and improved effectiveness.
Quality confirmation rule
Establish milestones, from development to start of production, and confirm conformance with six quality items when production processes change.
Design Review (DR) function strengthening rule
Register DR plans with quality risks of medium or high level as important DR subjects with participation of company-wide DR reviewers. The General Manager of the Corporate Quality Management Dept. holds company-wide DRs for cases with a particularly high risk level.
Quality monitoring rule
Monitor and share information company-wide with respect to quality status changes or problems concerning manufacturing or markets. Manufacturing defects and customer complaints are shared company-wide every month through reports to the Corporate Quality Management Dept., and the appropriateness of countermeasures is discussed.
Rule for handling major customer complaints
In the event of a serious customer complaint, including a potential complaint, the situation is promptly reported to the Quality Committee Chair to formulate company-wide countermeasures.
QRE-P Activities
We have been promoting QRE-P activities* throughout the NGK Group. Through these activities, we can identify business procedures in the realization of products and services in order to eliminate risk while improving quality. Since the start of QRE-P activities in FY2017, we have worked to incorporate the QRE-P concept into quality systems in each department, and also have provided practical training so that the person in charge can put QRE-P in practice, using development projects as examples.
In FY2023, we began to make improvements in line with rules we established in FY2022 that call on departments to analyze both technical measures and deficiencies in business procedures and improve their own systems when a failure occurs in the market. Moreover, with the aim of more effectively and efficiently eliminating quality risks in development projects, we strengthened the system of joining the research and development departments in considering quality risks in accordance with QRE-P from an early stage in development before commercialization. In addition, to boost expansion of QRE-P activities, we began to roll out QRE-P activities to Group companies outside Japan as well as Group companies inside Japan.
In FY2024, we plan to further entrench the rules we established in FY2022 calling on departments to analyze deficiencies in business procedures and improve their own systems. Moreover, we will further encourage examination of risks together with the research and development departments from the early stages of pre-commercialization development. We also plan to actively promote QRE-P activities at Group companies outside Japan.
QRE-P (Quality Risk Elimination Process): An operational protocol intended to more effectively eliminate quality-related risks at every stage when bringing products to market, from product planning to mass production.
Activities to Strengthen DR Functions
The increasing and diversifying quality demands from customers call for the integration of knowledge among various members throughout the development process, not only from the design department but also from the manufacturing and production engineering departments. For this reason, the NGK Group considers the Design Review (DR) to be the most critical activity. DRs are conducted when development milestones are reached or when production processes change. Critical DRs are conducted by reviewers from throughout the company to support the elimination of quality risks.
The DR Guidelines were created to promote DR discussions and to thoroughly eliminate quality risks. We are constantly enhancing the effectiveness of DRs through efforts to spread these guidelines company-wide, including awareness and review of each DR.
Furthermore, NGK organizes a company-wide DR (quality review meeting) for quality issues that are difficult to solve by one department. At this meeting, relevant engineers and experts from across the company discuss broad aspects of issues related to the reliability and safety of products.
We are also deploying the above-mentioned QRE-P approach to facilitate improvement of design level at the pre-DR period as well as to ensure the more effective utilization of organizational knowledge and experience from DRs.
Flow of DR Activities
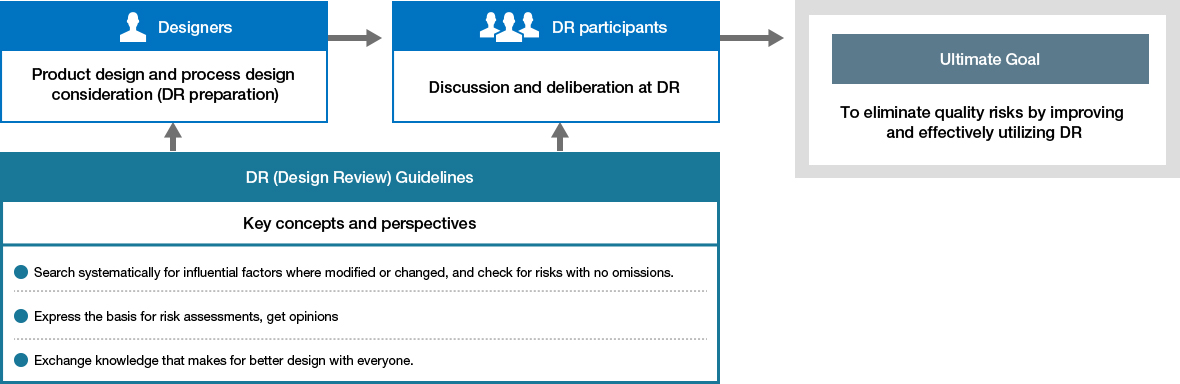
System for Considering ESG During Product Design
We design and develop products and services in accordance with the NGK Group Corporate Business Principles and Code of Conduct. As we strive to comply with the requirements of our customers and supply chain, we consider ESG by designing and developing quality management systems in accordance with the concept of QRE-P and the requirements of international standards (ISO 9001, IATF 16949, etc.). Output which takes into account QRE-P concepts like QFD and FMEA is shared and deliberated through Design Review (DR) and other examinations by those involved at the appropriate stage of development. In addition, we check implementation status through periodic internal audits of our quality management systems, and with audits conducted by our customers, supply chain, and certification authorities.
Quality Improvement Activities
QuiC Activities
Since 2003, the NGK Group has held QuiC (Quality up innovation Challenge) quality improvement activities in which all employees participate. These activities consist of quality improvement activities by small groups or individuals and suggestions that strive to enhance the quality of products, services, and work; best practices are then shared by the entire NGK Group. Every July, NGK holds a company-wide contest at its headquarters to highlight examples of outstanding improvement activities with the intent of horizontal expansion throughout the company.
Plus, since FY2021, we have revised our proposal evaluation methods to prioritize content in addition to quantity.
In July of FY2023, we held the Company-wide QuiC Activities Contest. Due to the COVID-19 pandemic, we held both physical and online versions concurrently. In October we held the NGK-BOX/Surprising Challenges! best practices presentation. NGK-BOX/Surprising Challenges! provides a company-wide forum for laterally sharing reform examples and model initiatives in order to boost employee motivation and invigorate the workplace. This was our fourth time to hold the event. Being able to hold this event in-person as well for the first time promoted communication between participants and helped to further increase motivation.
In FY2024, we will continue these activities, and pursue further quality promotion activities that all employees will take part in.
Suggestion Activity Participation Rate
FY2020 | FY2021 | FY2022 | FY2023 | |
---|---|---|---|---|
Manufacturing Department | 93% | 82% | 89% | 88% |
Non-manufacturing Department | 83% | 71% | 76% | 69% |
Clerical Department | 50% | 25% | 27% | 26% |
Number of suggestions | Approx. 19,000 | Approx. 16,400 | Approx. 15,600 | Approx. 14,500 |
Excellent Proposal Ratio | 17.8% | 18.2% | 20.7% | 24.5% |
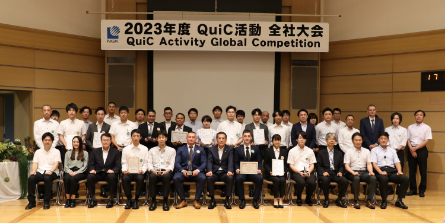
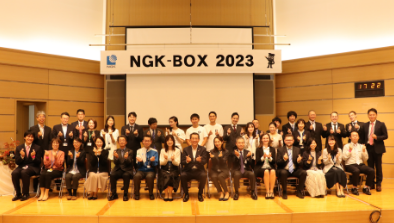
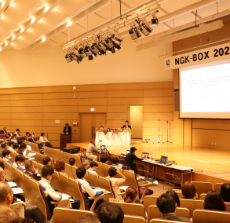
We held the best practices presentation “NGK-BOX/Surprising Challenges!” at the venue for the first time with a focus on bringing people together.
On-Site Training Inside and Outside Japan
For the first time in four years, we held overseas training that had been cancelled since FY2020 due to the effects of the COVID-19 pandemic. From November 4 through 11, the top nine recipients of the Outstanding Proposal Commendation and QuiC Excellence Award visited Poland and France to exchange opinions about improvement and experience foreign culture first-hand at NGK Ceramics Polska (ACP).
We resumed training inside Japan last year, and from December 13 through 16, nine recipients of the QuiC Excellence Award, Special Award, and NGK-BOX Excellence Award visited Okinawa to attend a nationwide QC Circle Conference and participate in discussion sessions about various topics, such as differences between NGK and other companies.
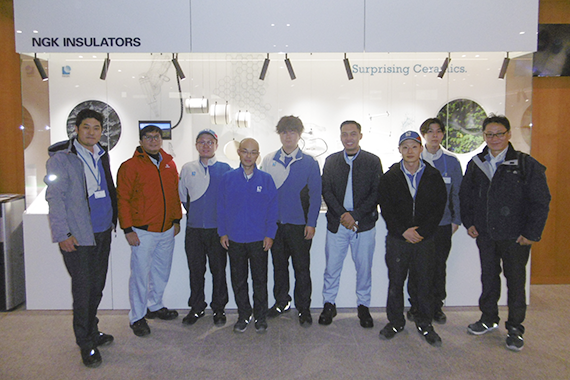
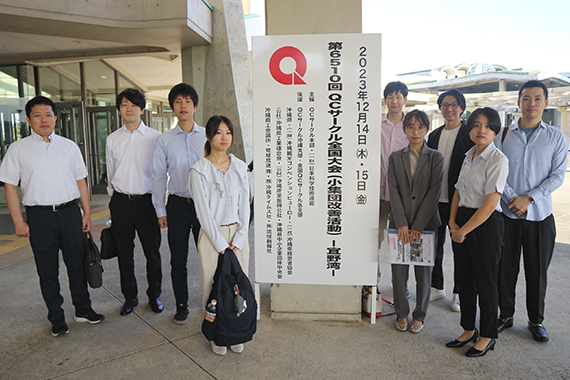
Quality-Related Education
Strengthening Quality-Related Education
The NGK Group aims to provide customers with products and services at a quality that exceeds expectations. Hence, we are continually working to improve the quality-related education that is given to all employees in order to ensure they are equipped with quality-related skills and greater quality-related awareness.
The primary educational activities include e-learning, face-to-face classes and through Microsoft Teams on themes such as level-based training for new and promoted employees, education in a wide range of fields from quality fundamentals to practical application, individual training on the themes of work issues and departmental needs, and basic statistical training to facilitate data utilization in collaboration with the Digital Transformation & Innovation Dept. We believe that training on quality management systems (QMS) to promote improvements in operational systems, and reliability training to establish activities that reduce quality risks (QRE-P activities) are of the utmost importance. And we aim to help employees acquire this experience through role playing and group discussions. We also try to support employment of statistical methods utilizing practical data. In FY2020, we began support activities for those taking QC tests, and the number of employees taking advantage of them has surpassed 1,300.
Quality-Related Education in FY2023
Training name | Number of participants | Objectives and key characteristics |
---|---|---|
Individual Training | 37 sessions |
|
QC Methodology Practice | 39 participants |
|
SQC (Statistical Quality Control) Methods Training |
A total of 83 participants |
|
Reliability Basics Training | Reliability Basics Training 1: 56 participants |
|
Reliability Basics Training 2: 53 participants |
|
|
Study of Failure and Methodology of Creation | Study of Failure Lecture: Approx. 250 participants Methodology of Creation Lecture: Approx. 150 participants Guidance and consultation: A total of 16 participants |
|
QMS Training | ISO/IATF standards interpretation: 726 participants |
|
ISO/IATF Internal Quality Auditor training: 196 participants |
|
|
VDA 6.3 Process Auditing Seminar: 42 participants |
|
Raising the Level of Maintenance Activities
With the aim of achieving a higher standard for maintenance activities and of improving productivity, a number of NGK Group employees in FY2022 took on the challenge of the Self-Maintenance Expert Test (Japan Institute of Plant Maintenance). This qualification is given to those who possess a broad range of necessary knowledge and skills concerning quality management, safety, and machinery maintenance, and are recognized as having the ability to plan and implement voluntary maintenance activities and provide instruction.
The NGK Group will continue encouraging employees to take the Self-Maintenance Expert Test as well as cultivate voluntary maintenance activities and stimulate greater employee motivation.
Number of Employees Who Passed the Self-Maintenance Expert Test
Company name | Number of Level 1 examinees | Number of employees who passed Level 1 (pass rate) | Number of Level 2 examinees | Number of employees who passed Level 2 (pass rate) |
---|---|---|---|---|
NGK | 33 | 11 (33%) | 34 | 24 (71%) |
NGK CERAMIC DEVICE | 5 | 4 (80%) | 55 | 36 (65%) |
NGK ELECTRONICS DEVICES | 7 | 1 (14%) | - | - |